
Processes
Types of Pulp Mills Operating in New Zealand
There are four types of pulp processing plants in New Zealand there are:
-
Mechanical - These make up 12.4% of New Zealands pulp output at 150,000 tonne
-
Kraft - These make up 74.3% of New Zealands pulp at 900,000 tonne
-
Thermo Mechanical - These make up 0.1% of New Zealands pulp at 830 tonne
-
Chemi Thermo Mecahnical - These make up 13.2% of New Zealands pulp at 160,000 tonne
There are five pulp mills in New Zealand these are:
Waste Produced from Pulp Process
The pulp and paper industry is a large consumer of fresh water and a significant source of wastewater, generated at various stages of pulping and paper-making, such as the debarking, chip-making, pulp manufacturing/bleaching, paper manufacturing and fiber recycling stages. The industry produces the third largest amount of wastewater after primary metals and chemical industries.
The industry produces 20 -100m^3 of wastewater per ton of air-dried pulp. This wastewater contains a variety of organic and inorganic contaminants that mostly originate from tannins (plant compounds), ligins, resins and chlorine compounds.
The objective of wastewater treatment processes is to remove contaminants using a series of physiochemical, biological and integrated treatment.
The treatment processes used in the pulp-paper industry however, produce solid sludge and greenhouse gases (GHGs) that have significant effect upon the environment and are subject to environmental regulations. Major GHGs, namely carbon dioxide, methane and nitrous oxide are produced in this industry.
Automation in the Pulp Mill
Making white pulp can be an expensive process, in terms of both chemical costs and environmental costs.
In the bleaching process, certain chemicals (traditionally chlorine) are added to a pulp mixture in order to change the colour in order to meet certain market standards. However, in chlorine dioxide stages, adding more chemicals past a certain optimum point may no longer produce a corresponding brightness response.
Online bleaching process analyzers and process controls have played a major role in reducing the use of expensive chemicals. They function by automatically measuring lignin content, which defines the amount of bleach required for a given run of pulp in order to remove it – feedback measurement of pulp brightness using other electronic sensors can then be used to alter chemical consumption as needed in order to manufacture pulp as efficiently as possible.
Automation also plays a role in minimizing safety issues within pulp mills within a pulp mill, there are numerous hazards to deal with. Exposure to these hazards depends upon the level of automation within a pulp plant. Historically, industrial and pulp production was a semi-automatic process which required a great deal of manual intervention.
For example, valves at the top and bottom of a batch digester would be manually opened, and during the filling stages gases in the digester would be displaced by incoming chips. Chemical levels would be adjusted according to experience rather than sampling, and adjusting the process would be dependent on the skill and knowledge of the operator. In modern mills manual control has progressed to electronic controlled pumps and valves, allowing for remote operation.
In addition to automatic digester capping valves and operator control rooms, other controls include local exhaust ventilation at batch digesters and blow-tanks, capable of venting at the same rate the vessel’s gases are released, negative pressure in recovery boilers to prevent gas leaks and continuous gas monitors with alarms where leaks may occur.
The different processes have difference conversion rates:
-
Mechanical Pulping- is able to convert 95% of the dry product to wood pulp
-
Chemical Pulping- is able to convert 40% to 50% of the dry product to wood pulp
-
Chemimechanical Pulping- is able to convert 80% to 90% of the dry product to wood pulp
-
Dissolving Pulp- is able to convert 35% of the dry product to wood pulp
How Much of the Wood Chip Can Be Converted into Pulp
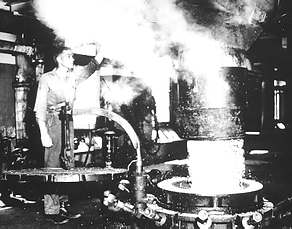

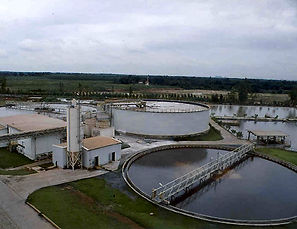
Written by: Christie O'Conner and Hayden Gardner